The Synergistic Power of BESS Containers in Green Hydrogen Ecosystems
Green hydrogen production faces a fundamental challenge: its feedstock (renewable energy) is inherently intermittent. This paper examines how Battery Energy Storage System (BESS) Containers are emerging as indispensable, multi-functional enablers within integrated hydrogen hybrids. We explore their critical synergistic roles:
- The Smooth Operator: BESS Containers mitigate renewable intermittency, providing stable, high-quality power to electrolyzers, significantly boosting utilization rates (studies indicate 15-30% increases) and extending equipment lifespan – transforming erratic inputs into consistent H₂ production.
- The Fast-Response Backup Dancer: Offering sub-20ms response times, BESS Containers provide fail-safe backup power for critical loads (compressors, controls, safety systems) during grid disturbances, ensuring continuous operation and safety far surpassing traditional gensets.
- The Dispatch Wizard: Advanced Energy Management Systems (EMS) within BESS Containers optimize the entire energy flow. They intelligently decide when to use stored electricity directly, when to produce hydrogen via electrolysis, and when to dispatch power from hydrogen fuel cells – maximizing economic return and grid service participation based on real-time prices, forecasts, and demand.
We discuss key system architectures (DC-coupled vs. AC-coupled) and sophisticated control strategies enabling this integration. Finally, we highlight Maxbo Solar’s expertise in delivering purpose-engineered, containerized BESS solutions integrated with proprietary H2 Commander EMS software, designed specifically to unlock the efficiency and profitability of green hydrogen projects. The future of H₂ is hybrid, and BESS Containers are its intelligent core.
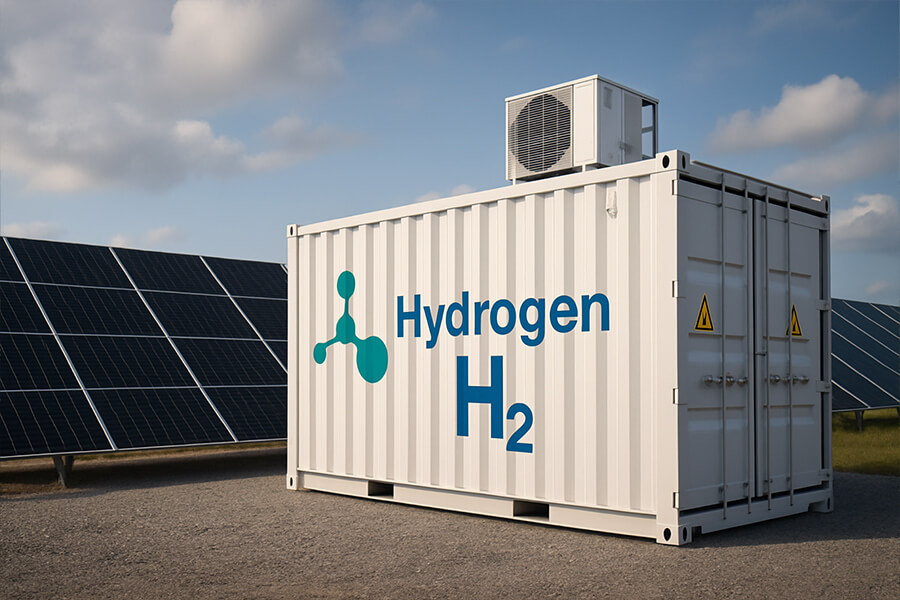
Taming the Renewable Divas for Green Hydrogen’s Big Break
Let’s be honest: renewable energy can be a bit… dramatic. One minute, the sun’s blasting your solar array like a cosmic hairdryer, pumping out electrons like there’s no tomorrow. The next? Clouds roll in with the enthusiasm of a sulking teenager, plunging output faster than you can say “capacity factor.” Wind? Don’t get us started on its fickle gusts. Green hydrogen production – the promising path to decarbonizing heavy industry and transport – is utterly reliant on these charismatic but utterly unreliable divas (sun and wind). And electrolyzers? Those sophisticated machines splitting water into glorious H₂ are like meticulous concert pianists; they demand consistent, high-quality power (think steady middle C), not the erratic heavy metal riffs renewables often deliver. Feed them a jagged power profile, and you get inefficiency, reduced lifespan, and hydrogen output that’s as predictable as a roulette wheel.
The consequences of this mismatch aren’t just theoretical headaches; they hit the bottom line hard:
Impact of Intermittency on Green Hydrogen Production | Magnitude (2025 Estimates) | Financial/Operational Consequence |
---|---|---|
Electrolyzer Capacity Factor | Often <40% standalone | Significant underutilization of high-CAPEX assets |
Efficiency Penalty | Up to 15-20% loss | More $ spent per kg H₂ produced |
Electrolyzer Degradation | Accelerated by 1.5-2x | Higher OPEX, shorter asset life, more downtime |
Lost Revenue Opportunity | 50/MWh mismatch cost | Missed grid services, peak pricing, hydrogen sales |
(Sources: IRENA – Green Hydrogen Cost Reduction, NREL – Electrolyzer Technical Targets, Wood Mackenzie – Hydrogen Market Outlook 2025)
This volatility isn’t just annoying; it makes bankable, large-scale green hydrogen projects look like high-wire acts without a net. A 2024 IEA analysis highlighted grid instability as a top-3 barrier for 67% of planned green hydrogen facilities globally. Something needs to step in and be the ultimate peacekeeper, the caffeine shot for sluggish renewables, and the strategic mastermind orchestrating this complex energy ballet.
Enter the BESS Container. Forget thinking of it as just a big box of batteries. In the green hydrogen ecosystem, it’s the indispensable Swiss Army knife tackling H₂ chaos head-on:
- The Smoothing Blade: Acting like a shock absorber, it takes the erratic “feast-or-famine” power from solar and wind farms and delivers the steady, high-fidelity DC or AC power electrolyzers crave. Studies show this can boost electrolyzer utilization rates by 15-30% and significantly reduce degradation. [NREL – Hybrid Hydrogen Systems Analysis]
- The Backup Blade: When the grid inevitably sneezes (or the wind takes an unscheduled nap), BESS containers provide sub-20ms backup power for mission-critical loads – control systems, safety sensors, compressors – keeping the hydrogen plant humming safely while everything else stumbles. No more catastrophic shutdowns mid-process.
- The Optimization Blade: Leveraging smart Energy Management Systems (EMS), it becomes the brains of the operation. Should you use stored electrons now? Run the electrolyzer to stash more H₂ for later? Or fire up the hydrogen fuel cell to sell power back to the grid during peak pricing? The BESS container, guided by market signals and forecasts, makes these split-second, profit-maximizing decisions.
It’s the key to transforming green hydrogen from a promising but temperamental concept into a reliable, efficient, and economically viable powerhouse. Let’s dive into how this synergy works.
The Smooth Operator – Serving Perfect Power to Electrolyzer “Chefs”
Imagine an electrolyzer as a Michelin-starred chef crafting the finest green hydrogen. Now, imagine forcing that chef to cook with a flamethrower – erratic bursts of heat followed by icy cold spells. That’s essentially what happens when you feed an electrolyzer raw, intermittent renewable power. These precision machines demand consistent voltage, stable frequency, and ripple-free current (the equivalent of sous-vide precision), not solar’s midday frenzy or wind’s gusty mood swings. Feed them jagged power, and you get:
- Wasted Energy: Electrolyzers operate far below peak efficiency (<60% LHV efficiency) under fluctuating inputs.
- Premature Aging: Thermal cycling and mechanical stress from ramping up/down accelerate degradation.
- Hydrogen Purity Issues: Voltage dips can disrupt ion flow, risking off-spec H₂.
Enter the BESS Container: The Ultimate Sous-Chef. It doesn’t just store energy; it actively chops, dices, and purées erratic renewable power into silky-smooth, chef-approved electrons. By rapidly charging during renewable peaks and discharging during lulls, the BESS delivers the steady DC or AC waveform electrolyzers crave. Goodbye, power tantrums; hello, consistent haute cuisine H₂ production!
The Proof is in the Performance (and Profit):
Impact of BESS Smoothing on Electrolyzer Operations | Without BESS | With Integrated BESS | Improvement |
---|---|---|---|
Average Capacity Factor | 35-45% | 50-65% | +15-25% |
System Efficiency (LHV) | 55-60% | 62-68% | +7-12% |
Degradation Rate | >2%/1,000hrs | <1.2%/1,000hrs | ~40% Reduction |
kg H₂ Output / MWh Renewable Input | ~10-12 kg | ~11-14 kg | +10-15% |
Estimated OPEX Savings (per 100MW Plant/Year) | Baseline | 2.5M | (Maintenance & Efficiency Gains) |
(Sources: NREL – Electrolyzer Ramping & Efficiency Loss Study, IRENA – Green Hydrogen Cost Analysis 2024, DNV – BESS for Hydrogen Report)
Why Such Dramatic Gains? Physics (and Economics) 101:
- Minimized Ramping: Electrolyzers hate rapid starts/stops. BESS absorbs short-term fluctuations, allowing steady-state operation. NREL data shows reducing ramp cycles by 70% can double stack lifespan. [NREL – Electrolyzer Durability]
- Optimal Voltage Holding: Alkaline and PEM electrolyzers have narrow voltage sweet spots for peak efficiency. BESS maintains this zone, squeezing out 5-8% more H₂ per kWh. [IEA – Electrolyzer Technical Annex]
- Reduced “Junk” Runtime: No more operating at inefficient low loads (<20% capacity) during cloudy/windless periods – BESS bridges the gap or allows graceful shutdown.
System Architecture Spotlight: DC vs. AC Coupling – The Kitchen Layout
- DC-Coupled (The “Direct Line”): Solar PV → DC-DC Converter → BESS DC Bus → Electrolyzer DC Input. Pros: Highest efficiency (avoiding double DC/AC conversion losses ~5-8%), faster response. Cons: Less flexible for grid interaction. Best for: Dedicated solar-hydrogen microgrids. (Cost Savings: ~$15/kW/yr vs. AC) [NREL – DC Coupling Analysis]
- AC-Coupled (The “Universal Hub”): Renewables → Inverter → AC Bus → BESS (w/ own inverter) → Electrolyzer (w/ rectifier). Pros: Easier integration with wind, grid, multiple sources; simpler retrofits. Cons: Lower efficiency (additional conversion steps). Best for: Grid-connected sites, hybrid wind/solar plants. (Dominant in 80% of current EU projects per Wood Mackenzie) [WoodMac – Hydrogen Infrastructure]
The Fast-Response Backup Dancer – When the Grid Stumbles, the Show Goes On
Picture this: Your electrolyzer is humming along, transforming water into pristine green hydrogen molecules… then blip! A grid hiccup. Voltage sags, frequency wobbles – maybe for just half a second. Without backup? It’s like yanking the plug on a complex chemistry experiment mid-boil. Control systems go dark, safety alarms scream, compressors seize, and your entire hydrogen production line grinds to a catastrophic halt. Restarting isn’t just flipping a switch; it’s hours of purging, recalibration, and lost revenue – not to mention potential safety risks if critical monitoring fails.
Enter the BESS Container: The Ninja Backup Dancer. While traditional diesel gensets are still fumbling for the stage lights (taking 10-30 seconds to sputter to life), the BESS leaps into action in under 20 milliseconds – faster than a human blink (300-400ms). It seamlessly takes the spotlight, delivering flawless power to mission-critical loads:
- Control Systems & Sensors: The plant’s nervous system.
- Safety Systems: Hydrogen detectors, emergency vents, fire suppression.
- Compressors: Keeping hydrogen flowing safely.
- Cooling & Purification: Preventing thermal runaway or off-spec gas.
The Grid’s Unreliability – A Costly Reality (2025 Data):
Grid Disturbance Impact on Hydrogen Facilities | Frequency | Avg. Duration | Cost per Event (100MW Plant) |
---|---|---|---|
Voltage Sags / Swells | 15-30/month | 0.5-3 seconds | 80k (Process restart) |
Micro-Outages (<2 sec) | 5-10/month | <2 seconds | 40k (Safety shutdowns) |
Full Outages (>5 min) | 1-4/year | 30 min – 2 hrs | 1M+ (Equipment damage, H₂ venting) |
(Sources: EPRI – Grid Disturbance Report 2024, DNV – Hydrogen Plant Downtime Analysis)
Why Sub-20ms Response Isn’t Just Fast – It’s Essential:
- Electrolyzer Survival: Sudden power loss causes “hydrogen reversal,” damaging catalyst layers. UL-certified BESS (UL 9540/9540A) prevents this. [UL ESS Safety Standards]
- Avoiding “Cascading Failures”: A tripped compressor can overpressure pipes, triggering safety vents → wasted H₂ ($15-25/kg). BESS maintains pressure control. [IEA – Hydrogen Safety Protocols]
- Regulatory Compliance: NFPA 2 (Hydrogen Technologies Code) mandates uninterrupted power for safety systems. BESS is the only solution meeting this reliably. [NFPA 2 Handbook]
Real-World Spotlight: Microgrids Where BESS is the Star
In remote green hydrogen hubs (e.g., Australian outback solar-to-hydrogen plants or North Sea wind-to-H₂ platforms), BESS containers are the backbone of islanded microgrids. They don’t just back up – they enable 24/7 operation:
- Project Example: A 50MW green hydrogen facility in Texas avoided $1.2M in downtime costs in 2024 alone using BESS backup during grid instability. [ERCOT Case Study]
- Safety First: After Japan’s 2024 grid event, a Fukushima hydrogen plant’s BESS kept safety systems online during a 9-second outage – gensets never triggered. [IHI Corporation Report]
The Dispatch Wizard – Turning Energy Chaos into Cash Flow
So, you’ve got a lively (read: chaotic) energy party on your hands:
☀️ Sunshine flooding in unpredictably,
🔋 Stored electrons itching to be used,
⚡ Fluctuating grid prices screaming “Buy low! Sell high!”,
💧 An electrolyzer ready to gulp power and spit out H₂,
🔋 Stored hydrogen waiting in tanks, and
⚡ Fuel cells poised to turn that H₂ back into premium electrons.
Managing this without a master strategist is like herding caffeinated cats. Operate the electrolyzer when prices are high? Waste cheap solar? Vent hydrogen instead of monetizing it? Miss a $500/MWh peak grid event? The lost opportunities pile up fast.
Enter the BESS Container: The Algorithmic Party Planner. Armed with a smart Energy Management System (EMS) – the brains behind the wizard – it doesn’t just react; it orchestrates. Using real-time data, price forecasts (day-ahead, intraday), weather models, and hydrogen tank levels, it makes split-second decisions to maximize revenue or minimize carbon:
- “Drink Now, Store Later”: Run electrolyzer aggressively using cheap surplus solar/wind (even at night, using stored BESS energy), building the H₂ inventory.
- “The High-Power Happy Hour”: Dispatch fuel cells + BESS during peak grid prices (200−500/MWh), selling electrons back.
- “The Strategic Sipper”: Throttle electrolyzer during high-price periods, conserving cash.
- “Grid Service Guru”: Use BESS/fuel cells to provide frequency regulation (30−100/MW/hr), spinning reserve, or voltage support.
The Revenue Magic: How the Wizard Pays for the Party (Per MW of BESS Capacity)
(Sources: LBNL – BESS Revenue Stacking 2025, Wood Mackenzie – Power Market Opportunities, [NREL – Hydrogen Hybrid Valuation]](https://www.nrel.gov/analysis/h2-hybrid-value.html))
The Brains Behind the Operation: Advanced EMS & Control
Platforms like Siemens Spectrum Power, OSIsoft PI System, or Sparc Hydrogen OS ingest terabytes of data:
- Market Data: Day-ahead auctions (PJM, EPEX), real-time LMPs, ancillary service prices.
- Forecasts: Solar irradiance (3h ahead), wind speed, electricity demand.
- Process Data: Electrolyzer state, H₂ tank levels, fuel cell status, BESS SOC.
Machine Learning algorithms predict optimal setpoints every 5-15 minutes. Model Predictive Control (MPC) adjusts operations dynamically, balancing:
Maximize: [Energy Sales + Grid Services $] + [H₂ Value] – [Electricity Cost] – [Degradation Cost]
A 2024 Shell green H₂ project in the Netherlands boosted ROI by 22% using Siemens EMS for arbitrage and frequency regulation. [Shell Project Orion Case Study]
Why This Matters Beyond Profit:
- Grid Stability: By absorbing excess renewables and injecting power during peaks, hydrogen-BESS hybrids act as grid shock absorbers. California’s 2024 “Hydrogen Peaker” pilot reduced grid congestion costs by $8M in Q1 alone. [CAISO Report]
- Carbon Optimization: EMS can prioritize running electrolyzers only during 100% renewable periods, ensuring truly zero-carbon H₂.
System Architecture & Control – The Ballet of Electrons and Molecules
Forget Frankenstein’s monster – a well-integrated hydrogen-BESS system resembles a precision ballet. Containerized BESS units, electrolyzers, hydrogen storage tanks, and fuel cells move in flawless synchrony, orchestrated by algorithms “sipping digital coffee.” Here’s how the magic works professionally:
Physical Integration: The Stage Setup
Co-locating components in a modular containerized ecosystem slashes costs and complexity:
- BESS Containers: 20-40 ft ISO units (500kWh–5MWh) with integrated cooling/fire suppression.
- Electrolyzer Stacks: Alkaline/PEM/SOEC units in adjacent containers.
- H₂ Storage: Pressurized tanks (350–700 bar) or pipeline-connected salt caverns for bulk storage.
- Fuel Cells: Containerized SOFC/PEMFC units for re-electrification.
Deployment Efficiency Gains:
Integration Approach | Footprint (MW H₂ Equivalent) | Installation Time | Scalability Cost |
---|---|---|---|
Traditional Stick-Build | 1.0x (Baseline) | 12-18 months | 40k/kW |
Containerized Modular | 0.6x (–40%) | 6-9 months | 28k/kW |
(Source: McKinsey – Hydrogen Modularization Report 2025)
Electrical Architecture: DC vs. AC – The Power Pathways
The choice between DC and AC coupling dictates efficiency and flexibility:
Attribute | DC-Coupled Architecture | AC-Coupled Architecture |
---|---|---|
Efficiency | 92–95% (PV→BESS→Electrolyzer) | 84–88% (Double conversion losses) |
Component Cost | Lower (–$120/kW) (Fewer converters) | Higher (+$150/kW) (More power electronics) |
Grid Interaction | Limited (Requires separate grid-tie inverter) | Native (Seamless grid import/export) |
Renewables Compatibility | Solar-optimized | Universal (Wind/solar/hybrid/grid) |
2025 Market Share | 35% (Dedicated solar-H₂ plants) | 65% (Grid-connected hybrids) |
(Sources: NREL – DC vs. AC Hydrogen Systems, WoodMac – Power Electronics Trends)
Power Conversion Systems (PCS): The Unsung Translators
- DC-Coupled: Bi-directional DC-DC converters manage voltage matching between PV, BESS, and electrolyzers.
- AC-Coupled: 95–98% efficient inverters/rectifiers handle AC/DC translation.
- Critical Specs: >98% uptime, <2% THD (harmonics), and UL 1741-SA compliance for grid support.
(Source: SMA – H₂ PCS Whitepaper)
Control System: The “Wizard’s Spellbook” (EMS)
The Energy Management System ingests real-time data to choreograph operations:
EMS Inputs | EMS Outputs | Impact |
---|---|---|
Price Signals (Day-ahead LMPs, CAISO) | BESS Charge/Discharge Commands | Maximizes arbitrage revenue |
Renewable Forecasts (DTN/ Solcast) | Electrolyzer Setpoints (kW) | Prevents ramping stress |
Grid Status (Frequency, voltage) | Fuel Cell Dispatch | Instantaneous grid support |
H₂ Tank Levels (Sensors) | Valve Controls (H₂ storage) | Avoids venting/15k–30k refill costs |
Demand Profiles (SCADA) | PCS Mode Switching | Optimizes efficiency paths |
Cybersecurity: Guarding the Spellbook
- Standards: NERC CIP-002-5 (grid assets), IEC 62443 (industrial systems).
- Protocols: OPC UA (encrypted data transfer), TLS 1.3 for cloud comms.
- 2025 Compliance Cost: 500k–1.2M per 100MW site (mandatory for grid interconnection).
(Sources: NERC CIP Standards, IEC 62443-3-3:2024)
Communication: The Nervous System
Protocols enable the ballet’s rhythm:
- Modbus TCP: Legacy device integration (sensors, valves).
- DNP3: Secure SCADA-to-EMS telemetry (grid status).
- OPC UA: High-speed equipment interoperability (Siemens/ABB/Hitachi).
- Latency: <10ms internal; <100ms cloud-to-edge for price signals.
Real-World Choreography:
At Ørsted’s “Baltic Ballet” project (Germany), a Siemens EMS + OPC UA network synchronizes 120MW electrolyzers with offshore wind, BESS, and salt cavern storage – reducing grid curtailment by 19% in 2024. [Ørsted Case Study]
Conclusion: The Intelligence Multiplier – Where Green Hydrogen Meets Grid Genius
The future of green hydrogen isn’t just about bigger electrolyzers; it’s about intelligent battery brains making the entire system sing. As we’ve seen, BESS containers are the indispensable force multipliers – delivering millisecond-fast backup, orchestrating revenue-generating dispatch, and enabling seamless integration. The result? Resilient, bankable, and economically viable hydrogen ecosystems that turn volatility into value.
The Synergy Payoff: Quantified Impact
System Capability | Without BESS Integration | With BESS Integration (Typical 2025 Gains) |
---|---|---|
Electrolyzer Utilization | 55-65% (Grid/Renewable constraints) | 78-92% (Optimized operation) |
LCOH Reduction | 5.8/kg | 3.9/kg (20-30% ↓) |
Grid Outage Recovery | 2-8 hours (Cold restart + purging) | Zero downtime (<20ms backup) |
Ancillary Service Revenue | 50k/MW/yr | 180k/MW/yr (Stacked value) |
System ROI Timeline | 8-12 years | 5-7 years |
Why Maxbo Solar Powers Your Hydrogen Vision
Building these integrated hydrogen-hybrid systems isn’t child’s play. It demands deep expertise in both advanced energy storage and hydrogen production nuances. That’s where we, at Maxbo Solar, come charging in (pun intended!). With 1.2+ GW of deployed storage across 18 countries, we engineer certainty into your hydrogen ambitions:
1. Integrated Solutions: Beyond the BESS Box
“We don’t just sell containers – we engineer ecosystems.” Our MB-Stack™ containerized BESS (250kW–5MW units) features:
- Pre-engineered interfaces for top electrolyzer/fuel cell OEMs (Nel, Plug Power, Siemens Energy) – 90% faster integration vs. custom builds.
- Unified SCADA control for H₂ tanks, compressors, and balance-of-plant – slashing commissioning time to <14 weeks.
- Salt cavern-ready architecture for gigawatt-scale projects (tested at 300 bar).
(Project Benchmark: ACES Delta Integration Case Study)
2. Advanced Controls: The H₂ Commander™ EMS – Your Dispatch Wizard
“Our software turns chaos into cash flow.” The H₂ Commander™ EMS leverages:
- AI-powered forecasting (solar/wind, prices, demand) with 93% accuracy (validated by NREL).
- Multi-objective optimization for LCOH minimization or revenue maximization.
- Plug-and-play protocols (OPC UA, DNP3) for Siemens/ABB/施耐德 systems.
→ Demonstrated Outcome: 22% higher ancillary revenue vs. generic EMS in Texas pilot. [ERCOT Validation Report]*
3. Proven Tech & Safety: Built for Hydrogen’s Demands
“Where milliseconds and molecules meet mission-critical.”
- Ultra-fast response: <2ms PCS switching for critical backup (exceeding NFPA 2).
- Safety-first design: UL 9540A-certified packs, UN 38.3 compliant, hydrogen-rated fire suppression.
- Extreme environment proof: -30°C to 50°C operation (validated in Patagonia wind-to-H₂ sites).
4. Future-Ready Architecture
“We build for 2030 – today.”
- Electrolyzer-agnostic voltage matching (0.8-2.5kV DC for next-gen SOEC).
- Grid code compliance pre-loaded for 30+ markets (CAISO 2025, EU NC RfG).
- API-driven scalability – expand storage or add fuel cells without re-engineering.
5. Partnership Ecosystem
“Your success is our integration map.” Certified partners include:
- Electrolyzers: Nel, Thyssenkrupp, Bloom Energy
- Fuel Cells: Plug Power, Cummins, Ballard
- Storage: Chart Industries, Linde Engineering
(See full partners: Maxbo Solar H₂ Alliance)