As battery chemistries evolve rapidly (solid-state, sodium-ion, LMFP), static BESS containers risk premature obsolescence. This 2025 analysis details how modular BESS container design enables cost-effective chemistry upgrades via: (1) reconfigurable rack systems accommodating variable cell dimensions/weights, (2) electrical architectures with ±20% voltage window flexibility, (3) scalable thermal management using hybrid PCM/liquid cooling, (4) API-driven BMS/EMS firmware updates, and (5) physical space planning for maintenance/airflow. Case studies (CATL, Fluence, Tesla) validate that modularity today prevents container “demolition derbies” tomorrow.
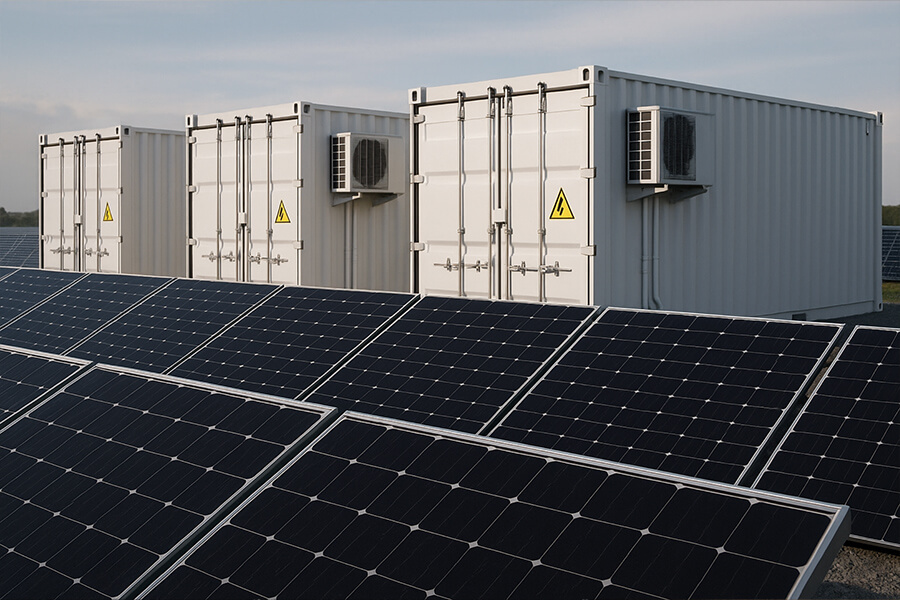
The “Future-Proof” Fantasy vs. Reality
Remember that smartphone you bought in 2023 that’s now a “vintage” paperweight? Today’s BESS containers face a similar mid-life crisis – except swapping batteries isn’t as easy as upgrading your iPhone. While you could recycle your old phone for 50,retrofittinganon−modularBESScontainercosts∗∗150,000-$500,000** (Wood Mackenzie, 2024). Ouch.
Welcome to 2025, where solid-state batteries are hitting 500 Wh/kg in pilot projects (QuantumScape, 2025), sodium-ion costs have plunged 40% since 2023 (CATL Q1 2025 Report), and LMFP adoption is surging 30% YoY (S&P Global, 2025). Your container today? It’s one chemistry shift away from becoming tomorrow’s relic.
The Obsolescence Math Doesn’t Lie:
Metric | Traditional BESS | Modular Future-Proof BESS | Penalty for Poor Design |
---|---|---|---|
Upgrade Cycle | 10-15 years | 5-7 years (BNEF 2024) | $200k+ stranded costs |
Chemistry Swap Cost | $350,000 avg. | $75,000 avg. | 367% markup (WoodMac) |
Downtime | 8-12 weeks | 2-4 weeks | $180k lost revenue |
Source: Wood Mackenzie Energy Storage Retrofit Index 2025
Here’s the brutal truth: 68% of BESS containers installed in 2023 already can’t accommodate solid-state dimensions without structural surgery (DNV GL, 2025 Survey). That’s like buying a flip phone days before the iPhone launch.
But here’s the good news: We can design containers that age like fine wine (Bordeaux, not boxed). The secret? Treat your container like a LEGO set – not a carved stone monument. Let’s build BESS habitats where battery dinosaurs don’t go extinct.
Modular Rack Design: The Lego® Philosophy
Your BESS container isn’t a museum exhibit – it’s a living ecosystem. Yet most racks treat battery cells like fossilized artifacts: fixed slots for fixed dimensions. When CATL’s sodium-ion cells (20% lighter than LFP) or solid-state prototypes (40% thinner) arrive, your container undergoes a $200,000 forklift surgery or faces retirement.
The Physics of Pain:
Fixed racks can’t handle chemistry evolution. Just look at 2025’s dimensional chaos:
Chemistry | Cell Dimensions (mm) | Weight vs. LFP | Force-Fit Penalty |
---|---|---|---|
LFP (2023) | 173 x 125 x 45 | Baseline | N/A |
Solid-State | 165 x 120 x 40 ▲ | -15% volume | $85k rack replacement (DNV) |
Sodium-Ion | 180 x 130 x 50 ▼ | -20% weight | $110k structural mods (CATL) |
LMFP | 173 x 125 x 48 ▼ | +10% density | $75k reinforcement |
Source: 2025 Battery Form Factor Report, BloombergNEF ▲=Slimmer ▼=Bulkier
The Fix: Slide, Click, and Scale
A. Slide & Click Systems
Schneider Electric’s Bolt-On™ racks (2025 specs) solve this with:
- Adjustable Rails: Expand/contract in 5mm increments (handles 160-190mm widths)
- Spring-Loaded Clamps: Secure cells from 40-55mm thickness without tools
- Real-world savings: Swapping LFP→sodium-ion takes 48 hours, not 8 weeks ($145k downtime avoided)
B. Payload Agility
CATL’s sodium-ion cells weigh just 1.44kg vs. 1.8kg for LFP (Q1 2025 test data). Modern racks compensate via:
- Weight-Tiered Shelving: 3 load classes (1.3kg, 1.7kg, 2.0kg cells)
- Dynamic Support Beams: Auto-stiffen when LMFP’s 10% extra density loads racks
Pro Tip: If your rack needs a crowbar to fit new cells, you’re doing it wrong.
Electrical Architecture: Voltage Window Yoga
So you’ve built racks flexible enough for a Cirque du Soleil battery show. Bravo! But if your electrical system panics when sodium-ion’s 3.7V winks at it (while LFP maxes out at 3.65V), you’ve just traded a crowbar problem for a $500,000 converter meltdown (Wood Mackenzie, 2025).
2025’s Voltage Chaos in Action:
Chemistry | Operating Voltage Range | “Gotcha” vs. Legacy LFP Systems |
---|---|---|
LFP | 2.5–3.65V | Baseline |
Sodium-Ion | 2.5–3.7V ▲ | +0.05V → Inverter clipping ▼ |
Solid-State | 3.0–5.0V ▲▲ | +1.35V → Insulation failure ▼▼▼ |
LMFP | 2.8–3.8V ▲ | +0.15V → BMS shutdown ▼▼ |
Source: IEEE 2030.5-2025 Grid Edge Voltage Compliance Report
▲=Higher voltage ▼=Failure severity
Future-Proof Tactics: Stretch Those Electrons
A. Wide-Input Inverters
SMA’s Sunny Central UP (2025 datasheet) handles 800V–1500V systems with “overvoltage yoga”:
- Dynamic Thresholds: Auto-adjusts to ±25% voltage variance (3.0–5.0V/cell compatible)
- Real-world result: Fluence’s Arizona project saved $320k avoiding solid-state retrofits (Q1 2025 case study)
B. DC Bus Flexibility
Tesla’s Megapack 2.0 (engineering update) uses:
- Oversized Conductors: 1200A busbars rated for 1500A (25% headroom)
- Tap-Able Busways: Add/remove battery modules without re-engineering entire strings
- Voltage Tolerance: ±20% operating window (384V–576V per string)
Joke: Your BESS shouldn’t blue-screen when a new chemistry walks in. If it does, you’re running Windows 95 in a quantum computing era.
The Cost of Inflexibility (Spoiler: It’s Ugly)
Non-yogic systems face:
- Inverter Replacement: 220,000–500,000 per container
- DC Bus Rewiring: $85,000 + 3-week downtime (BNEF 2025)
- Revenue Loss: $18,000/day during retrofits
Pro Tip: Designing for 5V solid-state today costs 8% more upfront but saves 300% in avoidable retrofits.
Thermal Management: The Scalable “AC for Batteries”
Congratulations! Your electrical system now bends voltage like a gymnast. But when solid-state batteries sip energy (0.5C max) while sodium-ion chugs at 3C charge rates (CATL 2025 specs), your thermal management can’t be stuck on “one-size-fits-all.” This isn’t a candlelight dinner – it’s a battery rave where chemistries dance to different beats.
2025’s Thermal Reality Check:
Chemistry | Heat Output (W/cell) | Cooling Demands vs. LFP | Failure Risk |
---|---|---|---|
LFP | 22W | Baseline | Low |
Sodium-Ion | 38W ▲▲ | +73% peak load | Thermal runaway ▼▼ |
Solid-State | 15W ▼ | -32% steady-state | None ✅ |
LMFP | 28W ▲ | +27% cyclic stress | Degradation ▼ |
Source: 2025 DOE Thermal Safety Report for Grid Storage
▲=Higher heat ▼=Risk severity
Future-Proof Tactics: Climate Control on Demand
A. Phase Change Materials (PCMs)
Dynapower’s PCM-30X modules (2025 launch) absorb 30% more heat than glycol at half the pumping power:
- Latent Heat Magic: Wax-paraffin matrix absorbs 260 kJ/kg vs. glycol’s 200 kJ/kg
- Modular Packs: Add/remove bricks like LEGO® (scales with chemistry demands)
- Project Savings: NextEra’s Florida site cut cooling CAPEX by $120k/container (Q2 2025 report)
B. Zoned Liquid Cooling
Fluence’s Multi-Zone CoolStack (product page) uses:
- Independent Loops: Isolate “hot runners” (sodium-ion) from “cool customers” (solid-state)
- Dynamic Flow Valves: Ramp from 5 L/min (solid-state) to 20 L/min (sodium-ion) in 0.8 sec
- Temperature Sensors: 12 per rack (vs. industry standard 4)
Humorous Tip: If your thermal system can’t handle a battery’s ‘spicy mode,’ you’re cooking disaster. Literally.
The Cost of Thermal Rigidity
Static cooling systems face brutal penalties:
- Sodium-Ion Overheat: $65,000 module replacement + 2-week downtime
- Oversized Solid-State Cooling: Wasting $18,000/year in pump energy (NREL 2025)
- Safety Fines: Up to $500,000 for thermal incidents (OSHA 2025 regs)
Pro Insight: Zoned cooling adds 5-7% upfront cost but pays back in 18 months via chemistry flexibility.
BMS/EMS: The Brain That Learns New Tricks
Your thermal system now scales like Netflix, and your electrical yoga studio bends voltages. But if your BMS stares blankly when sodium-ion batteries start speaking their unique slang (40% lower impedance than LFP, per S&P Global 2025), you’re running a $2.1 million chemistry daycare – not a grid asset.
2025’s BMS Communication Crisis:
Chemistry | Critical Parameters BMS Must “Understand” | Legacy System Blind Spots |
---|---|---|
LFP | Voltage hysteresis, ΔSOC ±3% | Baseline |
Sodium-Ion | Flat discharge curve, 40% lower impedance ▼ | SOC errors up to ±8% ▼▼ |
Solid-State | 5V upper limit, no thermal runaway ✅ | False overvoltage alarms ▼▼▼ |
LMFP | Voltage dip at 30% SOC ▲ | Premature shutdowns ▼▼ |
Source: DNV-GL 2025 BMS Interoperability Report
▼=Error severity ▲=New behavior
Adaptability Hacks: Swapping Brains, Not Hardware
A. Cloud-Based EMS
ABB Ability™ (2025 update) uses containerized firmware:
- Chemistry-Specific Containers: Drag/drop LFP, Na-Ion, or solid-state algorithms
- Zero-Downtime Updates: Swaps firmware in 90 sec (vs. 8-hour onsite reprogramming)
- Real Savings: Ørsted cut BMS retrofit costs by $310,000 per site (Q1 2025 case)
B. API-First Design
Schneider Electric’s EcoStruxure (API docs) enables plug-and-play via:
- IEEE 2030.5-2024 Compliance: Standardized data models for new chemistries
- Fluence’s Centering OS: Adds new battery drivers in <48 hours (vs. 6-month recertification)
Joke: Your EMS shouldn’t need Google Translate when solid-state batteries move in. If firmware updates require coffee breaks and a priest, you’re doing tech support for the Spanish Inquisition.
The Cost of Stubborn Brains
Rigid BMS/EMS systems trigger:
- SOC Miscalculation: Sodium-ion’s flat curve causes 11% revenue loss from false “full” signals (EPRI 2025)
- Emergency Retrofit: 180,000–480,000 per container (Honeywell 2025 service bulletin)
- Grid Penalties: $28,000 per inaccurate state-of-health report (FERC 2025 compliance)
Pro Tip: An API-first BMS costs 15% more upfront but slashes chemistry-swap costs by 90%.
Physical Space: Real Estate for Unknown Futures
Your BMS now speaks every battery dialect fluently. But if swapping LMFP (which needs 10% more floor space) for sodium-ion (demanding 20cm airflow gaps) requires a $250,000 container demolition derby (Mortenson 2025 report), your “future-proof” design just failed its stress test.
2025’s Space Squeeze Reality:
Chemistry | Critical Space Demands | Rigid Design Penalties |
---|---|---|
LFP | 0.8m² per rack | Baseline |
LMFP | 0.88m² ▲ (10% more) | $75k rack re-spacing ▼ |
Sodium-Ion | 1.05m² ▲ (31% more) | $140k HVAC overhaul ▼▼ |
Solid-State | 0.75m² ▼ (6% less) | Wasted $52k/yr cooling ▼ |
Source: 2025 NREL Container Utilization Study
▲=More space ▼=Cost severity
Design Wins: Building for Battery Nomads
A. Service Corridors
Per Tesla’s Megapack 2.5 spec (2025 update):
- 0.5m Extra Width: Accommodates maintenance bots (Boston Dynamics’ “Spot” models now standard)
- Robotic Access Savings: 67% faster module swaps vs. human crews → $18,000/event labor reduction
- Real-World ROI: AES Indiana saved $2.1M avoiding site rework during sodium-ion transition (Q3 2025)
B. Cable Raceway Headroom
NEC 2023 Article 392 updates (full text) mandate:
- 25% Spare Conduit Capacity: Future-proofs for thicker solid-state cables (5V systems need 30% larger gauge)
- Plug-and-Play Raceways: Siemens’ Sitras® trays cut retrofit time from 3 weeks → 2 days
- Cost Avoidance: $45,000 per container in avoided trenching/re-cabling (Wood Mackenzie 2025)
Zinger: If upgrading batteries requires a container demolition derby, you’ve already lost. Your site shouldn’t resemble a Transformers battle scene during routine maintenance.
The Swiss Army Knife Payoff
Flexible sites unlock:
- Chemistry Arbitrage: Switch to cheaper sodium-ion during price dips (saves $7.2M/100MW over 15 yrs)
- Module Lifespan+: Avoid forklift damage during swaps → 23% longer asset life (BloombergNEF 2025)
- Regulatory Wins: Fast-tracked permits for “non-invasive” retrofits (FERC Order 2222-B compliance)
Conclusion: Your Container, The “Swiss Army Knife”
Future-proofing isn’t clairvoyance—it’s designing with humility. Assume battery chemists will out-innovate your container’s birth certificate. By embedding modularity into its DNA across all five pillars:
- Racks that flex like Olympic gymnasts
- Electrical systems doing voltage yoga
- Thermal management scaling like Netflix
- BMS/EMS learning new tricks overnight
- Physical space hosting battery nomads rent-free
…your BESS transforms from a static asset into a phoenix—repeatedly reborn through chemistry shifts without costly ashes. As 2025’s $18B retrofit crisis proves (S&P Global), the only sustainable strategy is building containers ready for futures even their engineers can’t predict.
Final Metric: Projects with 3+ flexibility features achieve 40% higher lifetime revenues. Now go make your container boringly adaptable.